A lot of parts will go through our shop daily. Each one is different from the other. Some are large while others are small. Some are aluminum, others might be steel or stainless. Then there are simple parts such as a heat shield, but then there are also very complex weldments and assemblies. A prime example would be a tube weldment frame that we make here.

They are used in the transportation industry to protect a hydraulic oil tank and other components (which we also make). We make these frames out of a variety of material, with the outer sides out of 1.5″ x 1.5″ steel tubes.
The way we are producing them now is getting the tubes a laser cut bend relief, bending the tube, then welding the gaps together along with additional parts for the frame. Finally, we finish with powder coating them for that nice glossy finish.
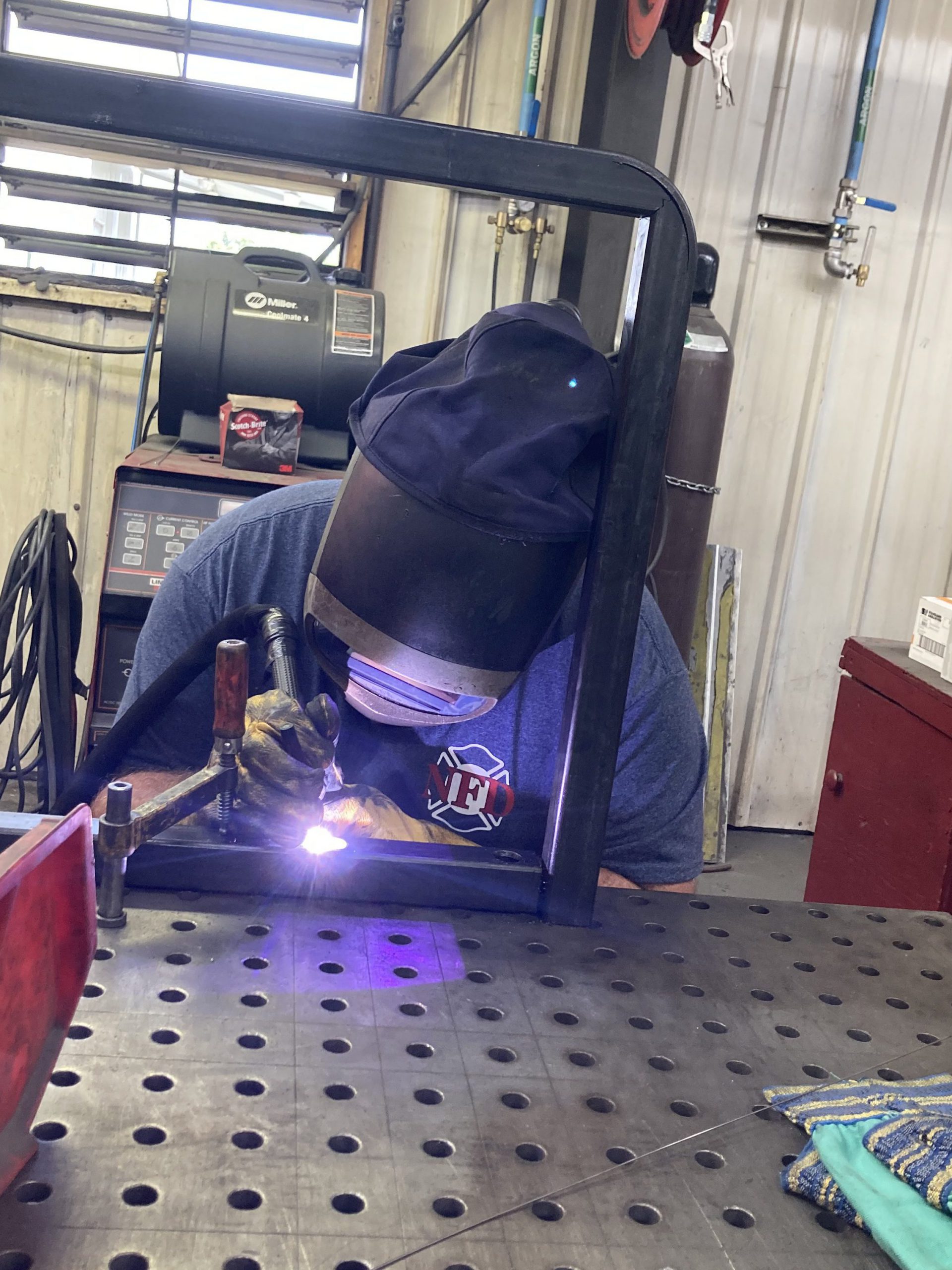
While this is the way we make them now. It wasn’t always like this. When we first started making these we would buy steel tubes and cast elbows. Then they would be all welded together, which was a lengthy process and required extensive fixturing.
Even if there wasn’t anything wrong, we knew that it wasn’t efficient. Each frame required a lot of handling and a lot of welding.
There were a few places we could start. It took a long time to weld. The cast elbows kept going up in price and being cast metal they didn’t weld as cleanly, nor powder-coated as nicely. So we sat down and brainstormed ideas on how to meet our customers’ expectations while making a better part more efficient. The main cost/time driver was welding all the elbows to the straight tube. It would be more cost-effective to be able to buy one tube and bend it in-house. The problem is that with the inner and outer radius requirements and the tube size/thickness, bending a tube just wasn’t going to work.
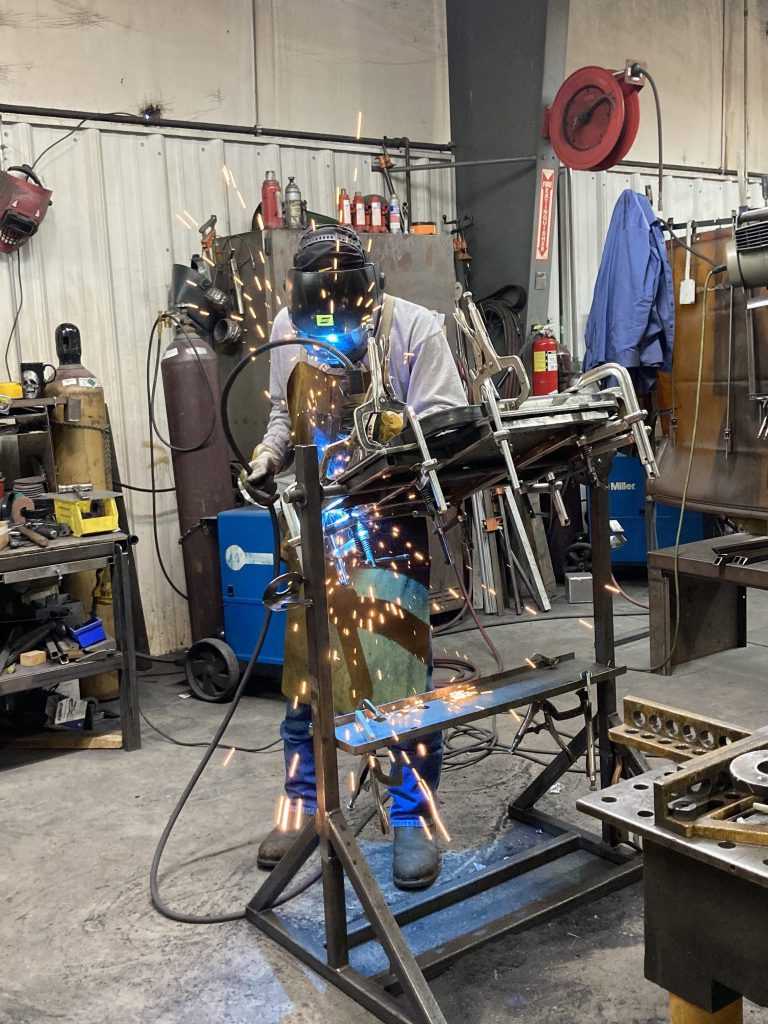
Our best option was to laser cut a bend relief. This allowed us to bend the rubes without crushing them. It also means the welders spend less time welding everything together. Instead of 9 individual pieces, we would now be able to make it out of one piece.
We worked closely with a tube-laser company to develop a good bend relief in the tube that would allow us to form each side of the frame out of one piece while keeping a nice, tight gap to make life easier for the welders. This frame also has some tight dimensional requirements, so we also had to make sure it would still meet print after forming and welding.
A drawing of a bend relief in one of our tube frames
As we continued, we noticed something else we could improve. It was tricky while forming to make sure the bend was at the right angle. So to help our benders we added a self-centering/locating notch. The notch would serve as a guide for the benders. This made the process both faster and accurate.
It’s these small details that separate us from our competitors. After years of operation, we have stayed true to both our customers and ourselves. We will continue to do what we specialize in, precision
Our quality policy states “IMEC is committed to producing quality products with continuous improvement to fulfill our customer’s needs and expectations.” There are two important words in our policy that relate to this particular project: Continuous Improvement. We are always looking at our processes to determine if there might be a better way and not being hesitant to try new things so long as the form/fit/function of the part isn’t jeopardized.